制御盤一貫製作のながれ
納入図面、製作図面を作成します。
製缶図を元に、読図・展開をして平板の板金状態から抜き加工、曲げ加工、溶接を経て塗装処理を行い、部品取り付け前の筐体を製作します。
図面から塗装完成品に金具、電気部品を取り付けて圧着加工済みの電線を配線します。
試験は必要な各項目を行い、出荷はシートで養生しご指定の場所・時間に納品します。
建設現場やプラント工場での、電気設備・計装設備・通信設備工事の配管、盤搬入据付、配線、端末処理・結線、総合試運転までを行います。
配電盤・制御盤・分電盤などの改造を現地へ出向いて行います。現地調査から盤内機器の容量変更・動作変更や機器更新などを行い、最終的には現地試験までを行います。
盤の製作仕様書と製造図面を作成するプロセス
納入図面、製作図面を作成します。
設計
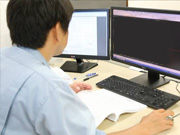
CADを使って納入図面(製作仕様,部品表,銘板表,外形図,内部機器配置図,結線図)を作成します。納入図面にて承認を頂きましたら,製作図面(製缶図,組立配線図)を作成します。
設計図、仕様書のデータを元に盤の筺体を製作するプロセス
製缶図を元に、読図・展開をして平板の板金状態から抜き加工、曲げ加工、溶接を経て塗装処理を行い、部品取り付け前の筐体を製作します。
NCプログラム
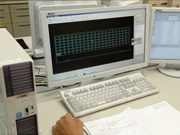
各種加工機を動かすためのプログラムを作成します。
図面に示された設計者の意図を実現するため、加工しやすい方法、品質、コストを考慮しながら読図し展開します。
パンチング加工
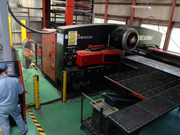
NCT(NCタレットパンチプレス)により、自動プログラムで数十種類の金型を駆使して外形ならびに穴あけ加工を行います。
ベンディング加工(曲げ)
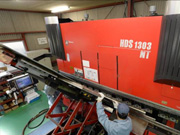
曲げ加工を行います。パンチング加工を施した部材を、平板から三次元形状(立体)にします。
溶接加工
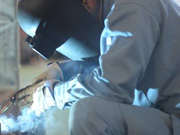
パンチング加工、曲げ加工された部材をTIG溶接機、半自動溶接機を用いて溶接加工を行います。
塗装
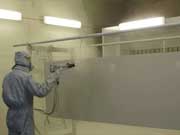
製缶が完了した製品を塗装します。環境に優しい粉体塗装を基本にしており、メラミン焼付け塗装も完備しております。
盤の筺体に、組立・配線をするプロセス
図面から塗装完成品に金具、電気部品を取り付けて圧着加工済みの電線を配線します。
フレーム組立
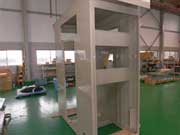
盤の筐体、フレーム部分を組み立てて、中に基板や部品を入れる前準備を行います。
電子機器の取り付け
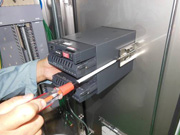
電子機器を取り付けていきます。
配線マークチューブ、デバイス作成
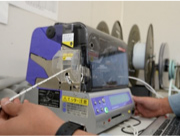
配線用マークチューブ、器具名称を作成します。
電線加工
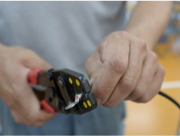
電線の測長データを作成し、切断・皮剥・圧着を行います。
配線(線出し・結線)
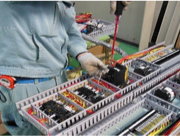
圧着加工済みの電線を配線ルートに這わせ(線出し)、端末を器具に取り付け結線します。
配線、増し締めチェック
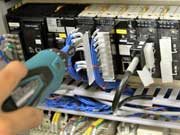
部品、端末処理の確認、増し締め、配線チェックを行います。
出来上がった盤が設計・仕様通りに組み上がっているか試験・出荷するプロセス
試験は必要な各項目を行い、出荷はシートで養生しご指定の場所・時間に納品します。
耐圧試験
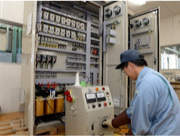
電路や機器の絶縁性能を確認し、最大使用電圧に応じ交流または直流で所定の電圧を規定時間印加し、電路に異常が発生しないことを確認します。
動作試験
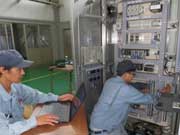
仕様書に基づいた回路通りに動作するかを確認します。
客先による品質検査
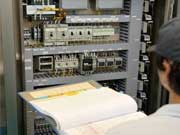
完成した製品の、数量、形状、寸法、外観、機能などに関し、発注企業様から適否を判定する検査を行っていただきます。
梱包、出荷
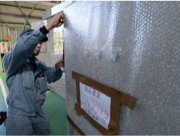
完成した盤を養生し、トラックに積み込み出荷します。
盤を現場で設置・試運転を行うプロセス
建設現場やプラント工場での、電気設備・計装設備・通信設備工事の配管、盤搬入据付、配線、端末処理・結線、総合試運転までを行います。
電線管配管(配線ルート)
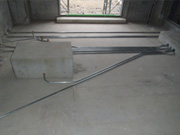
盤間、機器間に施工図を基に電線管を配管します。
現場搬入据付
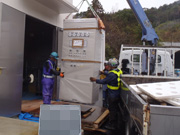
設計製作された盤を、クレーン等を使用し、現場に搬入据付します。
ケーブル配線
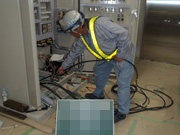
盤間、機器間に施工図を基にケーブルを延線、配線します。
端末処理・結線
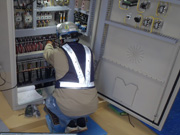
配線したケーブルを、配線図を基に端末処理、端子台への結線作業を行います。
動作試験・総合試運転
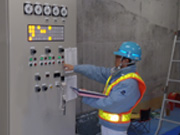
現地で、メーカー、自社設計立会の基に動作確認・総合試運転を行います。
調整作業や、アフターメンテナンス、納入後の仕様変更に対応する調査・改造を行うプロセス
配電盤・制御盤・分電盤などの改造を現地へ出向いて行います。現地調査から盤内機器の容量変更・動作変更や機器更新などを行い、最終的には現地試験までを行います。
現地調査
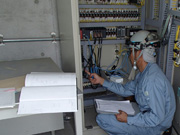
納入設置された製品、また既に稼働している設備、または増設などで、現場の盤を調査します。
現地改造(製造)
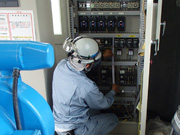
調査に基づき、現場の盤を改造する作業を行います。
現地調査(試験)
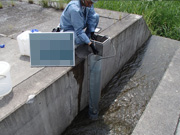
現地の運転調整作業を行います。※写真は水位計動作試験